Understanding The Safety Journey
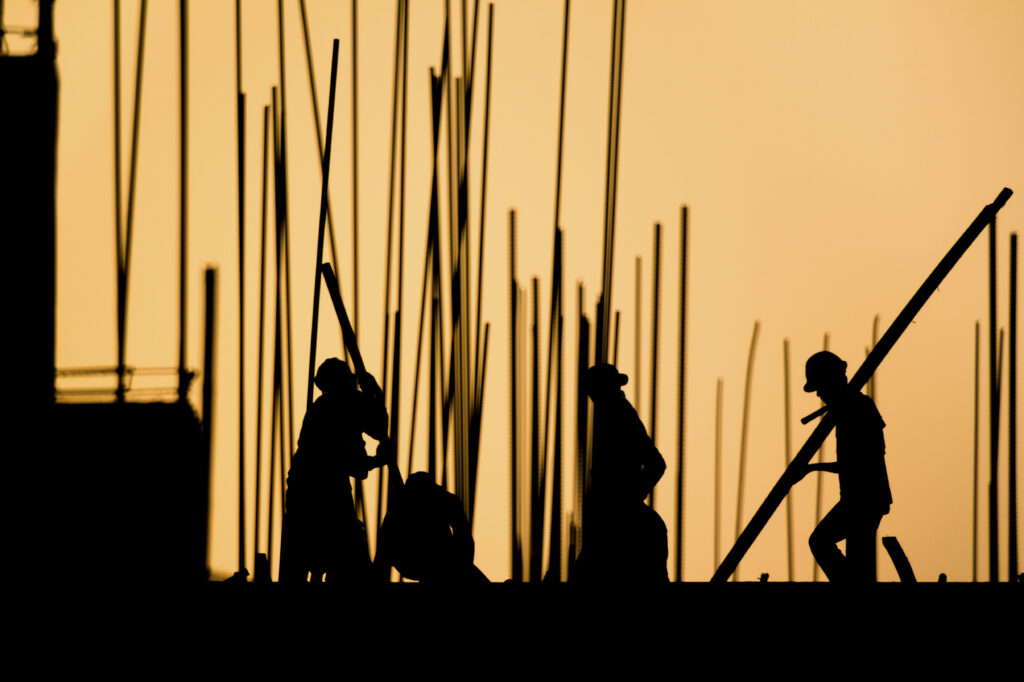
Improving safety performance within the power and utility industry has increasingly become the top priority for the majority of organizations across North America. It is a complex challenge of navigating the high-risk nature of the work amidst the challenging operating, compliance driven and transformative environment. Increasingly, companies are implementing an array of safety systems and protocols, including risk, stakeholder and safety management systems, along with robust human capital management programs. However, in many cases, safety performance is still plateauing and safety metrics, including perception surveys, injury frequency and severity rates are indicting a lack of forward progress.
We believe that regardless of current safety performance, there are three distinct phases of a power and utility organization’s safety journey, each with different strategies and unique characteristics. In simplistic terms, the three major phases include:
1 Eliminating intrinsically unsafe conditions: Focusing on physical conditions, tools, and equipment, and looking for opportunities to engineer unsafe conditions out of existence.
2 Developing safe work procedures and safety management systems: The specific procedures and systems industries use to reduce the potential for harm when dealing with hazards that can’t be completely eliminated, such as working with sources of energy.
3 Error reduction and human performance: Creating an environment in which the likelihood of errors is reduced, and reducing the potential for harm when inevitable human errors occur.
The challenge for most organizations lies in the overlapping nature of these three phases, each requiring very different types of management effort for success to occur. In companies that truly excel in safety, the principles involved in all three phases are well understood and, as such, the organization is able to apply the most appropriate response for the conditions present. A degree of success is often achieved with one particular approach to safety, but then safety performance “plateaus” and improvement stops. This does not mean there was anything wrong with the steps taken. The approach was appropriate for that particular phase of the safety journey, but it is not necessarily appropriate for the next one.
To explain why management’s approach must change between the three phases, it is useful to look at the commitment needed to achieve success in each phase. In phases 1 and 2, the typical approach to continuous improvement is through analyzing risk, developing action plans and obtaining commitment to completing the required actions. Management can insist on an audit of pinch points and have guards manufactured (phase 1). Similarly, management can insist on safe work procedures being written or a monthly safety audit being done, then hold people accountable to the completion of the activities (phase 2). Phases 1 and 2 respond well to a commitment to informed activity. However, in phase 3, management cannot stand in front of the workforce and seek commitment that employees will not make an error in the coming year. This highlights that management must think differently through the various phases of the safety journey.
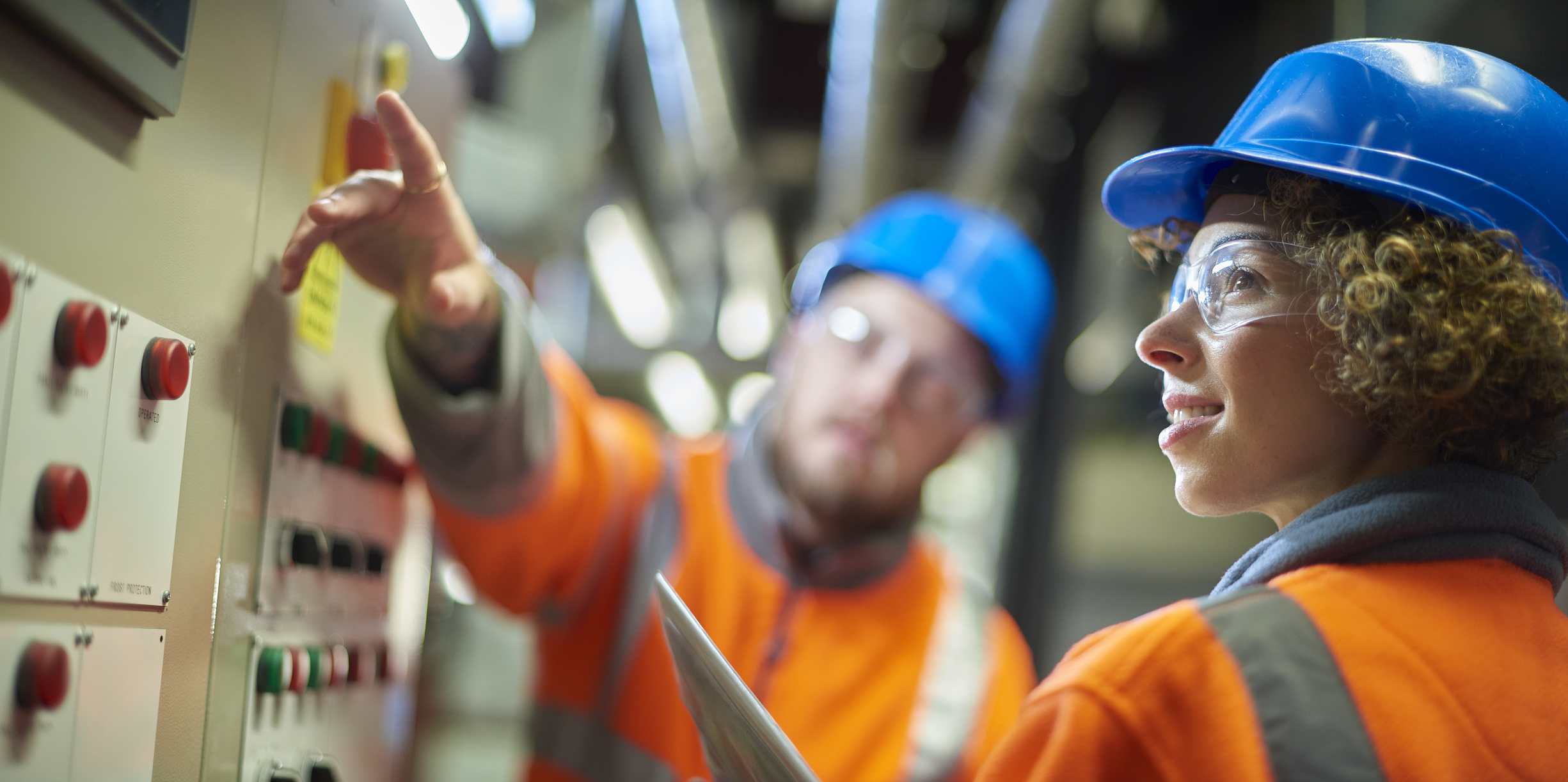
Where Safety Performance Stalls
Error Reduction and Human Performance
To date, power and utilities companies have typically been successful at achieving success in phases 1 and 2 of the safety journey; however, phase 3 is where safety performance typically stalls. The third phase of the safety improvement journey, error reduction and human performance, involves reducing the frequency and impact of normal lapses in mental focus and memory. True success in this phase involves strategies designed to positively influence the workplace and employees to reduce the potential for human error. Common examples include using a pre-flight checklist on an aircraft to reduce the potential for well trained pilots to make errors arising from the complexity of their tasks, or embedding specific safe work habits, such as applying lock-out/tag-out procedures and keeping personal workspaces free from clutter. Safety improvements in many companies plateau at this stage of the journey because of the unrecognized differences in what it takes to be successful at reducing errors when compared to engineering intrinsically safe equipment (phase 1) or creating safe work procedures (phase 2).
The Cognitive Disconnect
Reducing the number of errors made by otherwise well-intentioned employees and the harm that results requires an understanding of the way our minds work. The principles arise from cognitive psychology and the relationship between our conscious, subconscious, and unconscious minds. The conscious mind processes active thoughts and things we need to remember to do. The subconscious mind allows us to do things, such as walking to a destination without consciously th
Subscriber Access
Unlock Deeper Insights with The Engine Room
Join our community and gain exclusive access to our newsletter, full insights, thought leadership, and expert perspectives that shape our approach and principles. Dive deeper into the strategies that drive high-performing teams, leadership excellence, and operational success.
Sign up today to stay ahead with actionable knowledge designed to elevate your impact along with your organization and team.