Safety Performance Improvement
The Engine Room is an operational excellence firm with substantial expertise in evaluating safety performance, practices, the cultural drivers that affect safety results, and implementation strategies that drive safety outcomes. At The Engine Room, we understand our client’s commitment to protecting the public, employees, and the contractors it works with. This includes assessing opportunities to accelerate safety improvement journeys and mitigate Serious Injury or Fatality Potential (SIFP) while moving safety cultures and results to global best practices.
To create rapid and sustainable safety performance improvements, it’s essential to truly understand an organization’s safety performance barriers before prioritizing resources and efforts to generate the highest returns. The Engine Room’s methodology works to closely target the root causes of the safety challenges identified and the specific tools that will support accelerating safety performance moving forward. Our clients have extensive operational footprints with different operating groups and potentially different operating cultures. We believe it is imperative to identify and capture these differences to provide targeted findings and recommendations tailored to the specific gaps affecting an operating group, region, or culture.
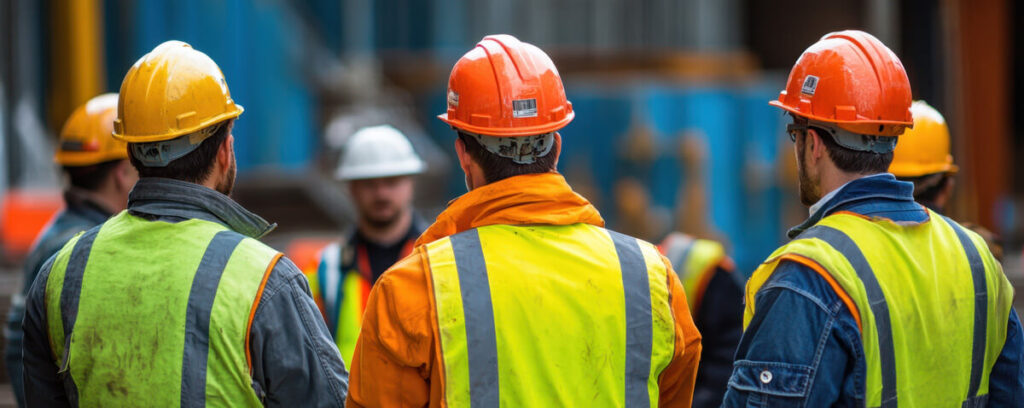
Tool 1: Operational Safety Diagnostic
The Engine Room’s Operational Safety Diagnostic (Safety Evaluation Process) is not a traditional safety audit. It provides a targeted evaluation of how an organization performs in all facets of safety performance, including safety strategy, culture, processes, leadership capability, management systems, training, metrics, and operational execution. This provides a concrete, unbiased identification of the management and employees’ current approach to operational safety and the improvement opportunities present. It identifies and assesses the root causes of current safety roadblocks and opportunities and prioritizes high-value target areas. Further, it determines the degree to which safety processes and systems conflict with or align with error reduction and human performance principles.
The ultimate objective of the diagnostic is to go beyond a review of the current operational conditions to provide leadership with an assessment of the primary underlying safety improvement challenges and recommendations designed to accelerate safety performance going forward. The multifaceted discovery includes tailored and candid one-on-one interviews with leaders and employees, direct observation of safety and work activities (including tailboards, worksite safety observations, safety inspections and safety meetings), and a review of safety system documentation, safety metrics and operational results.
The safety diagnostic is summarized in an Operational Safety Diagnostic report. The Report outlines the key findings, themes, and improvement recommendations from the evaluation process, including organizational safety strengths, challenges, and their root causes. The report’s conclusion presentation to senior leadership represents the conclusion of the diagnostic phase.
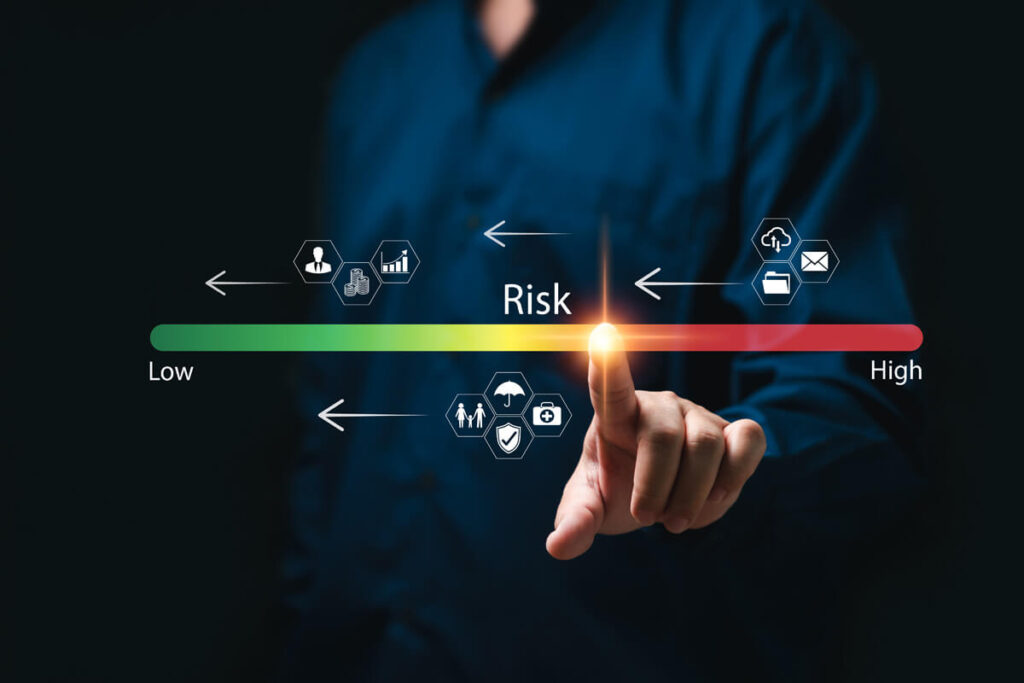
Tool 2: Organizational Safety Program Alignment and Acceleration
Following the completion of the Operational Safety Diagnostic, the focus inevitably shifts to how the Engine Room can best support the organization in achieving its organizational safety goals. The Engine Room believes in key principles for success surrounding strategizing improvement action plans. In particular:
- Target corrective actions at the root cause of the challenges and not the symptoms.
- Seek to leverage existing client company structures, practices, people, tools, and policies to the maximum extent possible before resorting to fundamentally changing significant features of the company’s current operating environment.
- Expect that changing practices and processes will require a blended learning process in which training, tailored coaching, and experiential learning may be needed to fill knowledge gaps and support safety leadership development.
Developing the implementation action plan involves critical steps, all of which build upon the results of the Operational Safety Diagnostic. The transition from the Diagnostic to the Implementation phase includes:
- The review of Safety Diagnostic findings, themes, and opportunities with senior leadership and critical safety support teams.
- Priority-setting sessions to identify the safety focus areas and leadership behaviours the implementation will target as the highest-value improvement opportunities. This includes creating alignment across departmental lines, operational leadership, safety, and human resources advisors.
- Alignment and or adjustments (if required) to safety management program elements, including safety processes, systems, audits or activities that may require restructuring or streamlining to achieve identified priority outcomes.
- Safety leadership training, coaching, and development for Leads, Supervisors, and Managers supporting the delivery of the target areas identified in the priority-setting sessions.
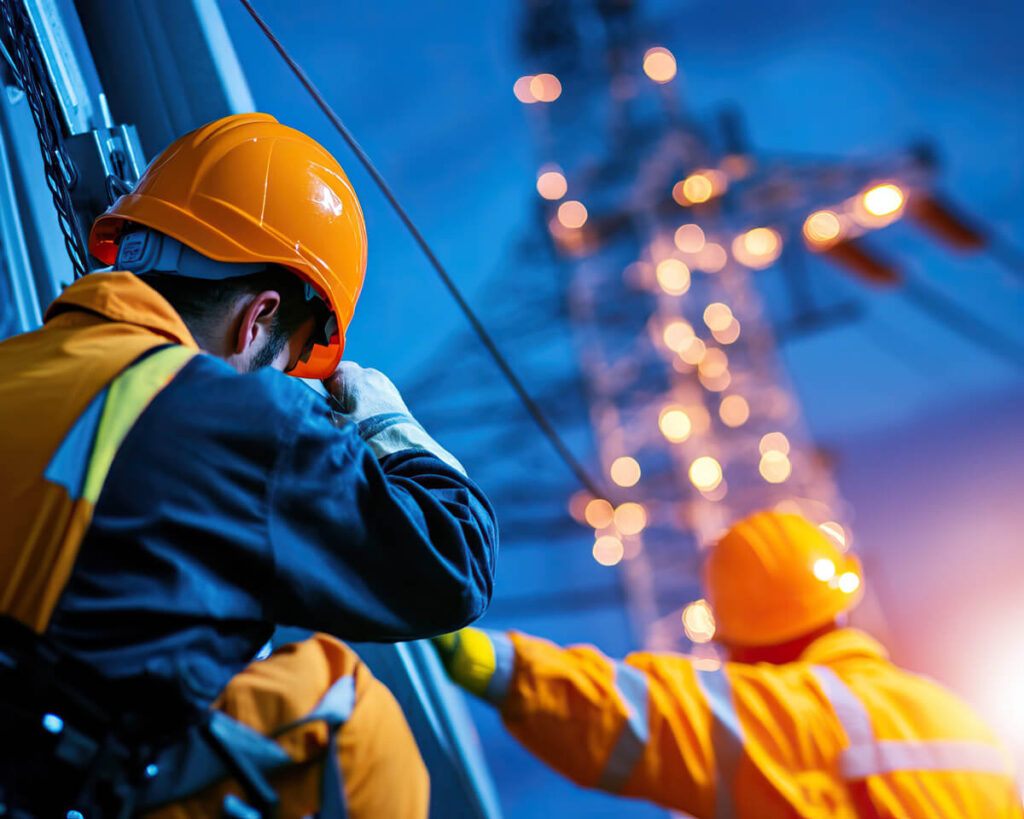
Tool 3: Safety Performance Implementation and Sustainment
At the Engine Room, all implementation plans are tailored to the precise cultural conditions and opportunities for improvement our clients face, and no two implementation plans are the same. This allows the Engine Room to provide cost-effective safety solutions with minimal disruption to the client’s operational cadence. While we allow the results of the diagnostic to inform implementation plans, common implementation examples and approaches include:
- Organizations looking to accelerate progress in their safety improvement journeys and mitigate Serious Injury or Fatality Potential (SIFP) while moving their safety culture and results to global best practices.
- Organizations with strong safety programs and process elements in place but the way individual activities have been implemented lack the quality required to achieve the desired outcome. Safety activities (i.e. WSO’s or FLRA’s) have become ‘tick-the-box’ exercises.
- Organizations in which there is a lack of clarity around the responsibility for safety between different departments in the company, such as Operations and the Safety Department, or between corporate, global or regional entities.
- Organizations in which the safety program is not the problem, as they suffer from a weak culture of accountability. Safety rules, procedures and practices exist but are simply not consistently followed.
- Organizations in which an aspect of leadership’s approach to safety is failing to resonate with employees. Common examples include excessive use of discipline, which drives reporting of safety issues underground, and excessive reliance on financial incentives to persuade employees to become safe.
In the majority of Engine Room safety improvement engagements, there is a focus on working with the Supervisors, Managers and Directors in the departments where employees are exposed to the most significant operational safety risks. While we refer to this activity generically as ‘Safety Leadership Development,’ we believe a ‘blended learning’ approach to safety leadership development of targeted training, tailored coaching, and experiential learning is the global best practice for achieving sustained behaviour change and increased capability. The field rollout of safety leadership application strategies and techniques increases their capability as safety leaders, contributes effectively to error reduction, and avoids the severe pitfalls that increase error rates in not correctly assessing risk.