The Role of Functional Specialty Departments
Historical Perspective
If we look back at the evolution of industry and leadership, it is apparent that the role of the Front Line Supervisor and for that matter the entire Operations Group in heavy industry is quite different today than it has been in the past. If we look back far enough, (say 100 years or so) we see that at one time the Front Line Supervisor ran their crew pretty much the way they wanted. In those days the Front Line Supervisor was able to operate as they saw fit, including how they hired or fired people. They were also responsible for holding people accountable to the production goals, setting safety standards as they saw fit, and environmental standards were not really much of a consideration.
Over time, industry and social standards have evolved and the role of the Front Line Supervisor and the Operation Group has had to evolve as well. One of the biggest shifts has been the rise of the Functional Specialists who have been developed to deal with specific aspects of the business that the Front Line Operations Supervisors and Managers cannot reasonably take care either due to a lack of expertise or time constraints.
This rise of the Functional Specialist in industry is really no different than what we see in the medical profession. 100 years ago, doctors were GP’s (General Practitioners). However with the advances in medical technology it became impossible for any GP to remain up to date on all medical developments. Consequently the medical profession has seen the rise of the medical specialist who tries to remain at the cutting edge of a particular aspect of medical technology. Today we have both GP’s and specialists serving complementary roles in the delivery of medical services. A good GP understands enough about the specialist’s areas of expertise that they know when they can treat the patient themselves and when they should bring in the specialist. Conversely a good specialist understands when the patient’s needs don’t align with their specialty and they defer to the GP or another specialist.
In industry this same evolution in standards created the requirement for a number of functional specialties. One of the first being the accountant and the development of the finance function in organizations. Over time we have seen the increased emphasis on safety give rise to safety specialists, the focus on the environment to environmental specialist and a host of other potential functional specialists such as Engineering, Maintenance, IT, Corporate Communication and a number of others.
A Depiction of an organization with functional specialists could look like the following:
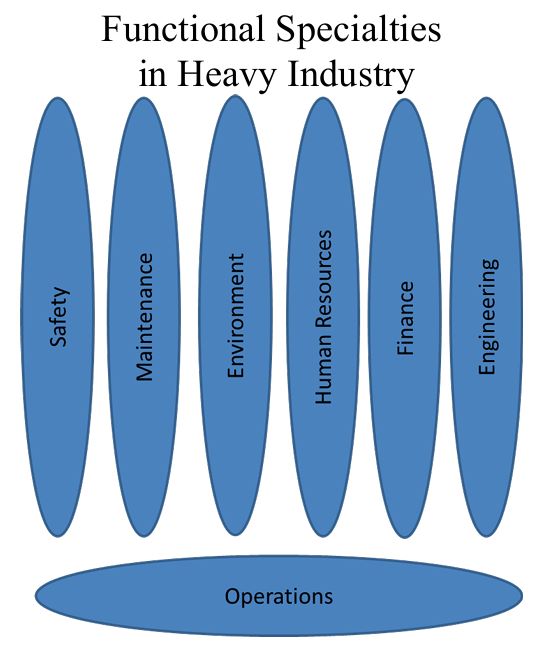
In the diagram above, the Operations Group is depicted as having expertise and responsibilities that are “broad” in nature but not too deep. Conversely, the responsibilities of the Functional Specialist are narrow in scope but very deep within that specialty.
Now that we have an organization with multiple groups in place to assist with delivering the organizational objectives, the question becomes, how do the functions interact with one another? One of the functions that have been subjected to the greatest amount of review in heavy industry is the role of the safety specialist. At one time the “Safety Supervisor” was seen as the person responsible for making sure the operation was conducted safely. This perspective has been effectively discounted in “best practice” literature. Today Industry is overwhelmingly convinced that best practice is for the Operating Group to be held accountable for the safety of their activities and their personnel. The Safety Specialist is a resource that the Operations Group should draw on in support of achieving their goals. The same logic can be found in the setup of virtually every functional specialty. For instance:
The Operating Group is accountable for their level of spending and the cost of production, not the Finance Group. |
The Operating Group is accountable for conducting operations to avoid spilling into the environment, not the Environmental Group. |
The Operating Group is accountable for providing the equipment to Maintenance for routine maintenance. Maintenance cannot just take the equipment when it suits them. |
With so much of the accountability for outcomes resting with the Operations groups in industry, it makes sense to explore just what the functional specialists are accountable for.
The Role of the Functional Specialist
Logically, companies will invest in Functional Specialties to support achieving specific goals, for instance Safety groups are expected to support elevating safety performance and Environmental groups support achieving environmental goals. However a significant complexity arises from the fact that while the Functional Specialists are responsible for supporting the achievement of aspects of the organizational goals, they are not accountable for what takes place in Operations
Subscriber Access
Unlock Deeper Insights with The Engine Room
Join our community and gain exclusive access to our newsletter, full insights, thought leadership, and expert perspectives that shape our approach and principles. Dive deeper into the strategies that drive high-performing teams, leadership excellence, and operational success.
Sign up today to stay ahead with actionable knowledge designed to elevate your impact along with your organization and team.